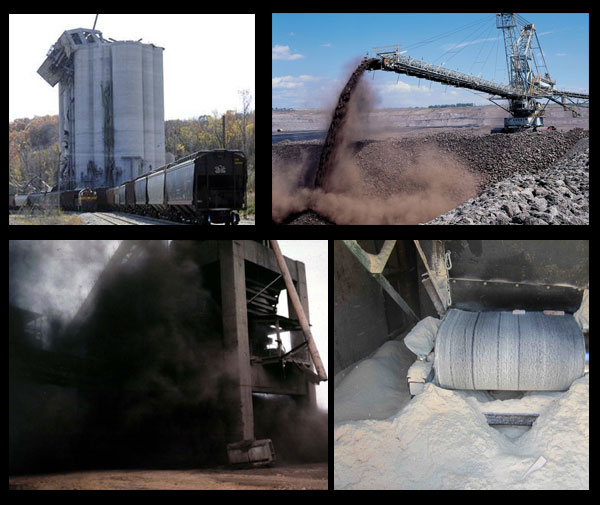
Disclaimer: Do not try this experiment unless you are highly trained in dust explosions, flash fires, and combustible material handling and safety incident response. Only qualified and trained safety personnel should attempt any experiment involving combustible materials. Jenike & Johanson does not recommend you recreate this experiment.
Perhaps I have your attention now that you’ve seen the photo of this fireball or the live-action flash fire we created with non-dairy creamer and a road flare. We ran this simple experiment in our parking lot this past week to demonstrate the combustibility of a common powder and its highly incendiary nature. Think about how freely we pour this powder in to our coffee!
As I approach my 20 year anniversary at J&J, I reflect on how many occasions I have come across combustible dusts at manufacturing sites around the world. I have visited over 300 plants, and knowing that 70% of dusts can form combustible mixtures, I have been in hundreds of situations where dusts could ignite under the right circumstances.
Many do not even realize the danger of combustible dusts. For example, look at the recent flash fire event in Taiwan whereby a concert involving 3 tons of colored corn starch was launched at attendees using air pressured cannons. Though the exact cause of dust cloud ignition is yet to be formally determined, over 40 cigarettes were found in the incident area, as well as non-explosion-proof lights.
As a reminder, a dust explosion requires five key ingredients, namely:
- combustible dust (sugar, plastic, wood, and most carbon containing dusts are combustible )
- oxidant (oxygen is present in air in process areas)
- ignition source (via static discharge, hot surfaces like heated bearings, or sparks)
- dispersion (dust can be readily emitted from numerous situations)
- confinement (silo, dust collector, dryer, mill/grinder)
It is scary to note that on several occasions I have witnessed the use of compressed air for cleaning surfaces with a combustible dust instead of vacuum collection. There have been many documented cases of combustible dust events in industrial plants whereby personnel have been killed or severely injured.
I have also witnessed heavily plugged dust collector ducts, whereby combustible dust has accumulated within the piping, which if an explosion occurs, can transmit the explosion to different parts of the plant. This situation occurred at the Foxcon plant where Apple laptops and IPads are polished. The aluminum dust accumulated in the duct work became “fuel for the fire” as the flame-front advanced through the plant.
Excellent guidance regarding dust explosions are available in National Fire Protection Association (NFPA) standards 652, 654, 68 (explosion venting), and 69 (prevention systems). Careful review of any new or existing combustible handling systems from a dust explosion and process safety basis should be performed by qualified personnel . NFPA 654 standard states that a combustible dust thickness layer of 1/32 in. (e.g., thickness of a paper clip laying flat; slightly less than 1 mm) is allowed under limited circumstances. However, if the dust has a high density, this limit may be reduced. I like the “general rule of thumb” whereby if you can write your name in the dust or if you cannot see the color of the paint below the dust, then immediate house keeping to pick up the dust is required – just do not let operators use a broom as this disperses the dust in the air!
Keep in mind that often the secondary explosion or building/structure collapse is what commonly causes the high casualty count. This is due to the primary explosion and its pressure wave knocking accumulated dust loose off beams, internal roofing, and equipment with hard-to-reach areas. This pressure wave is tremendously effective at dispersing additional combustible dust throughout a facility, which also has a fire underway as the perfect ignition source. It only takes a 1-2 psi (10 kPa) pressure wave to knock over a standard concrete block wall at a plant, thus, with explosion pressures exceeding 100 psi (6 – 7 bar) during a dust explosion, a block wall does not stand a chance for containing this pressure.
Jenike & Johanson engineers strive to design powder handling equipment that enforces reliable flow. Besides increasing process efficiency and yield, it also helps to avoid dust release since operators do not have to open up manways or access doors to poke, scoop, or aerate material to affect flow. This act generally releases dust and in the presence of an ignition source, and then – kaboom!
If you are not sure if your powder or dust can form a combustible mixture, a simple go/no go test can be run for about USD 500. More extensive testing can be run to accurately quantify your material’s explosivity behavior, as well as sensitivity to explosion from an electrostatic discharge.
Contact me if you need guidance on the dangers of combustible dust handling. As a reminder for safe handling of your powders, I recommend listening to the following song…