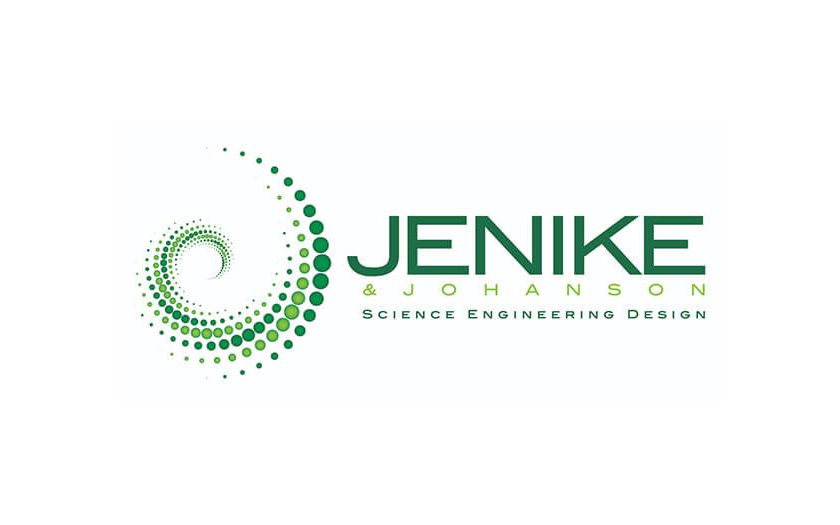
Originally as an employee of Apollo Technologies in 1976, and ultimately one of the founding owners of a Dallas based engineering services company (1982), Guardian Utility Services, Inc. (GUS, Inc.), I remember well discovering Jenike & Johanson’s (J&J) revolutionary “mass flow” concepts and material testing methods for characterizing bulk materials. Mass flow is an elegant idea which is now well accepted and seems obvious, but back when it was first introduced it was revolutionary. GUS, Inc.’s business base was most of the electric generating companies with coal fueled steam/electric generating plants, from the southeast U.S. across the south & southwest U.S. Some were “mine to mouth” operations, so GUS, Inc. did business at both the coal-fueled utility plants and the mines. What were Texas Utilities Generating Company and Texas Utilities Mining Company, and now Luminant, were significant customers of GUS, Inc.
TUGCO’s Big Brown Steam/Electric Generating Plant was just coming on line in 1976. Big Brown was the first “super critical” lignite fueled power plant in the world. It was experimental to the extent that it was 50% funded by the U.S. Department of Energy (DOE). Dealing with the quantities of lignite necessary to fuel a 550 megawatt generating plant and the fly ash & bottom ash created during the combustion process offered many engineering challenges. One of the plants operational disruption challenges was wet lignite. When lignite gets a little bit wet it is very sticky and won’t flow. I remember one of the plant operators saying, “When this stuff gets sticky you can throw it up in the air and it never comes down. It sticks up there somewhere.” Apollo and ultimately GUS, Inc. bought J&J Shear Testers and had Laboratory Test Trailers initially at Big Brown and also at Martin Lake Steam/Electric Generating Plant and Monticello Steam Electric Generating Plant after those plants were put into service. Our field people were trained by J&J and were running shear tests at the sites 24 hours per day, seven days per week during wet weather conditions. A data profile was developed and it could be accurately predicted when lignite was approaching disabling pluggage conditions. Apollo/GUS had developed a flow enhancer chemical product that improved the flow characteristics of wet lignite. The chemical product was applied based upon the shear value test data. This program virtually kept the TUGCO lignite plants on line during wet weather conditions. Ultimately, GUS, Inc. and J&J assisted TUGCO to replace the original funnel flow silo bunker discharges with mass flow design bottoms. With the good experience of working with J&J at TUGCO, GUS, Inc. often recommended J&J to other customers it did business with which were experiencing silo/hopper flow problems.
Both lignite and Powder River Basin Coal (PRB) have the potential to spontaneously combust if they sit dormant too long in the right conditions. This creates the risk of fires in silos and bunkers with serious safety/operational risks when lignite or PRB are placed in traditional funnel flow hoppers and the coal does not fully empty out on a “first in, first out” basis. As a result, J&J’s mass flow silo/bunker designs became critical to the safe and reliable operation of coal fueled steam/electric generating plants utilizing lignite and PRB coals.
In 2012, while working with Millcreek Engineering as a Project Manager related to a significant project with Barrick, we were asked to include J&J on the team to figure out the best manner to handle some particularly difficult to handle gold ore. J&J provided critical material testing information to help Millcreek Engineering and Barrick better understand the nature of potential ore handling problems resulting in designs to best deal with the issues.
Now I work for Jenike & Johanson, opening up an office in Northern Colorado to represent them. The good news was that I came to work for J&J with a pretty fair understanding of their long history, their solid reputation and the significant impact they have had on bulk material handling systems designs. Now as an insider to J&J, what I continue to be surprised with is the scope and breadth of the materials and industries they have worked with in the past and continue to work with every day. The broad ranging experience and knowledge of J&J’s people and the teamwork attitude continues to impress me as well. Now that I better understand the inner workings of J&J, I can’t imagine a bulk material handling issue where J&J could not contribute in a positive manner to understanding it’s “root cause” and how best to deal with it. I was always a fan of J&J, but more so than ever now that I am part of J&J.