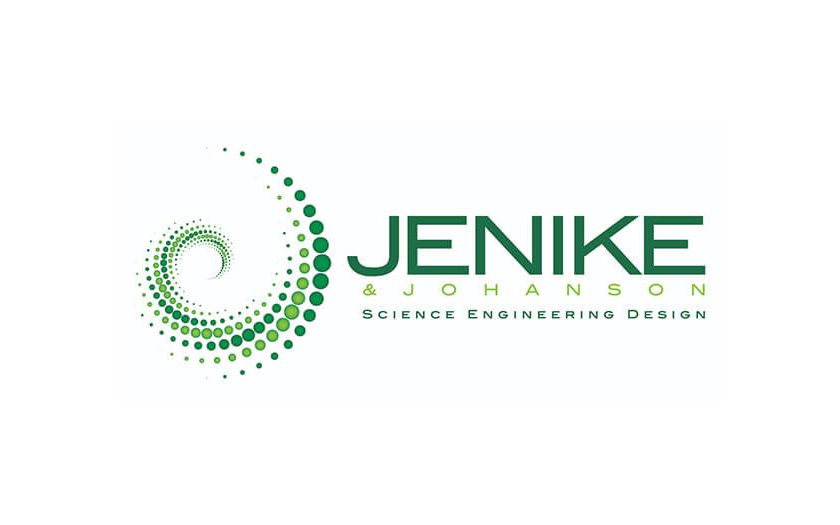
We at J&J often are pushing for mass flow to minimize segregation or other common flow problems – so how do you identify the flow pattern in your silo? After I had worked at J&J for a while, I got to go on a site visit. As I looked into the top hatch of a large petroleum coke silo (with a great view from up there- Long Beach Harbor), I was immediately struck by how much the flow pattern on the top surface mimicked the top surface of the models we build and run in our lab. It turns out that a free flowing material with a wall friction that is relatively independent of pressure exhibits the same flow pattern in a 20 foot diameter silo as it does in a 2 foot diameter model of that same silo – the flow pattern is pretty much independent of scale. For cohesive materials or very fine materials, it is more complicated. And the model friction needs to be similar to the prototype friction, which is not always easy to achieve.
To get back to mass flow or funnel flow- when looking at the top surface, if the granules at the wall are moving [1], then you have mass flow or, possibly expanded flow. Sometimes that top surface is deforming, in other words not all particles are moving downward at the same speed- usually the center is faster, we (J&J) still consider that mass flow. If the granules near the wall are dead static and a funnel type flow channel is formed in the center, then you have funnel flow.
Expanded flow is a condition when the lower converging geometry is not steep and smooth enough to cause material to slide upon it, yet the cylinder is tall enough and the flow characteristics are such that the central flow channel is cone shaped, and eventually reached the cylinders walls. From the top, material is moving everywhere, although there is static material below. An expanded flow pattern can look identical to mass flow from the top.
Sometimes the initial flow is mass flow, the stresses redistribute within the solids, and flow transitions to expanded flow and then funnel flow, often with a good couple of thumps along the way as large zones of material stop and start flowing. The flow pattern after this initial fill equilibration is the one causing the caking, segregation, or ratholing problems, so that’s the one that matters.
In the top of a mass flow bin, with a cylinder above the cone, particles tend to move in lock-step, what we call plug flow. As the bin empties and the level approaches the top of the cone, the pug flow behavior goes away and the velocity profile that is in the cone can be seen on the top surface. With a low level, material near the walls can travel substantially slower than in the center of the bin. It can be difficult to tell if the hopper is mass or funnel flow at this point.
Do you have mass flow, funnel flow, or expanded flow? Sometimes looking in the top is not possible – too dusty, not safe, or a lack of access. If you can inspect the bin interior walls while its empty, it is usually easy to tell if the walls have had material flowing against them. A secondary method is to drill a small hole – maybe 1/8”, in the hopper or silo, and then stick a broom straw through into the material while the silo is discharging. If the straw outside the wall moves up, then the material inside is moving down, and you have mass flow. It may be possible to do this at a number of levels at different times and identify a silo that switches between mass, funnel, and expanded flow – maybe if your material varies. Warning- Never drill a hole in anything without first determining that it is safe and will not cause a problem! “First” being the key word-
[1] It is surprising how good a human eye is at picking up the movement or non-movement of a surface against a wall, even at ultra-low velocities. I get the same impression on the freeway in judging if that car ¼ mile ahead is getting closer or farther away – I can usually tell even at very low speed differentials. When our ceiling fan shuts off, I can immediately “see” that it is slowing – although the blades are a total blur. Must be something we are just hard wired to do.