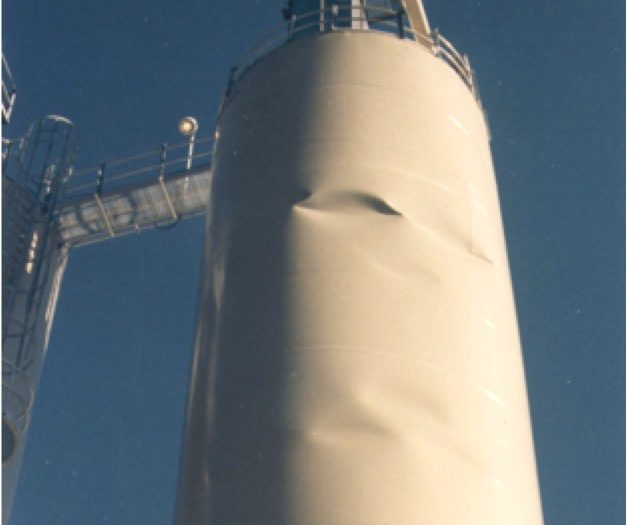
I will be presenting an article related to eccentric discharge from silos at the 2014 Structures Congress in Boston, MA, April 3-5, 2014. I thought about sharing a “blog” version of the article on our website, so here it is. For those attending the congress, you can join me for the presentation on April 3 as I discuss these fascinating structures and their behavior. Silos are one of the most critical pieces of equipment in industrial facilities and, at the same time, one of the least understood. When designing a process in an industrial plant, it is assumed that all bulk materials will be handled reliably. However, as these processes increase in complexity and size due to plant improvements and greater global demand for products, many storage silos are designed or modified to discharge eccentrically.
Even though those designs or modifications may meet all the requirements at the basic and functional engineering level for the envisioned process, they may have severe implications for the storage structural system, mainly in the form of failures. Failures in silos are costly as replacement and repairs of the storage structure are required, and personnel may be injured or even killed. Additionally, the downtime during this period translates into lost production as well as potential litigation.
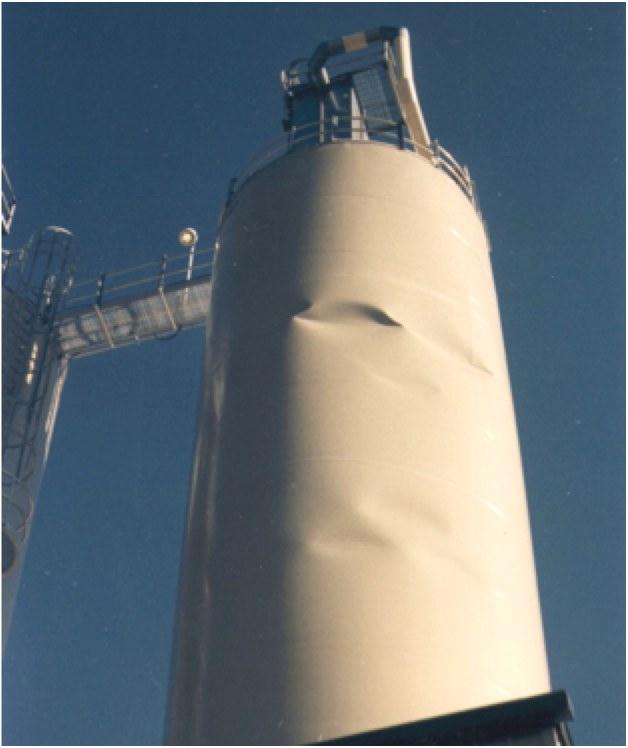
Eccentric discharge can occur with a mass flow or funnel flow pattern, but it is more common with funnel flow. In either case, the flow channel formation is not concentric with the cylindrical section of the silo. In the worst-case scenario, the flow channel intersects the cylinder wall and runs parallel to it until the free surface is reached. Eccentric discharge situations may be caused by silos discharging from one eccentric outlet or by multiple outlets not discharging at the same time. It can also be the consequence of gates or valves not properly operated (e.g., partially open) or improper design of a belt feeder interface or screw feeder. Asymmetric pressures develop on silo walls due to eccentric discharge. The most modern and comprehensive code on silo loads is commonly called “Eurocode” [British Standard BS EN 1991-4, 2006]. This code provides a procedure for calculating silo loads due to eccentric flow. If the resulting flow channel intersects the silo wall, non-uniform pressures will develop around the circumference of the silo, leading to circumferential bending and axial compression on the cylinder shell. The pressure normal to the cylinder walls in the flow channel is much less than the normal pressure developed in the surrounding bulk material. Furthermore, there exists a localized region of high pressure at the edges of the flow channel and the static material. Silo shells are efficient structures if internal pressures are applied uniformly. However, eccentric discharge changes the loading behavior to non-uniform pressures around the circumference of the silo. These non-uniform pressures cause high membrane stresses in thin metal silos, which may deform the shell and in some cases cause catastrophic failure. In concrete silos, these non-uniform pressures result in bending moments that may cause severe damage to the walls by developing dangerous cracks.
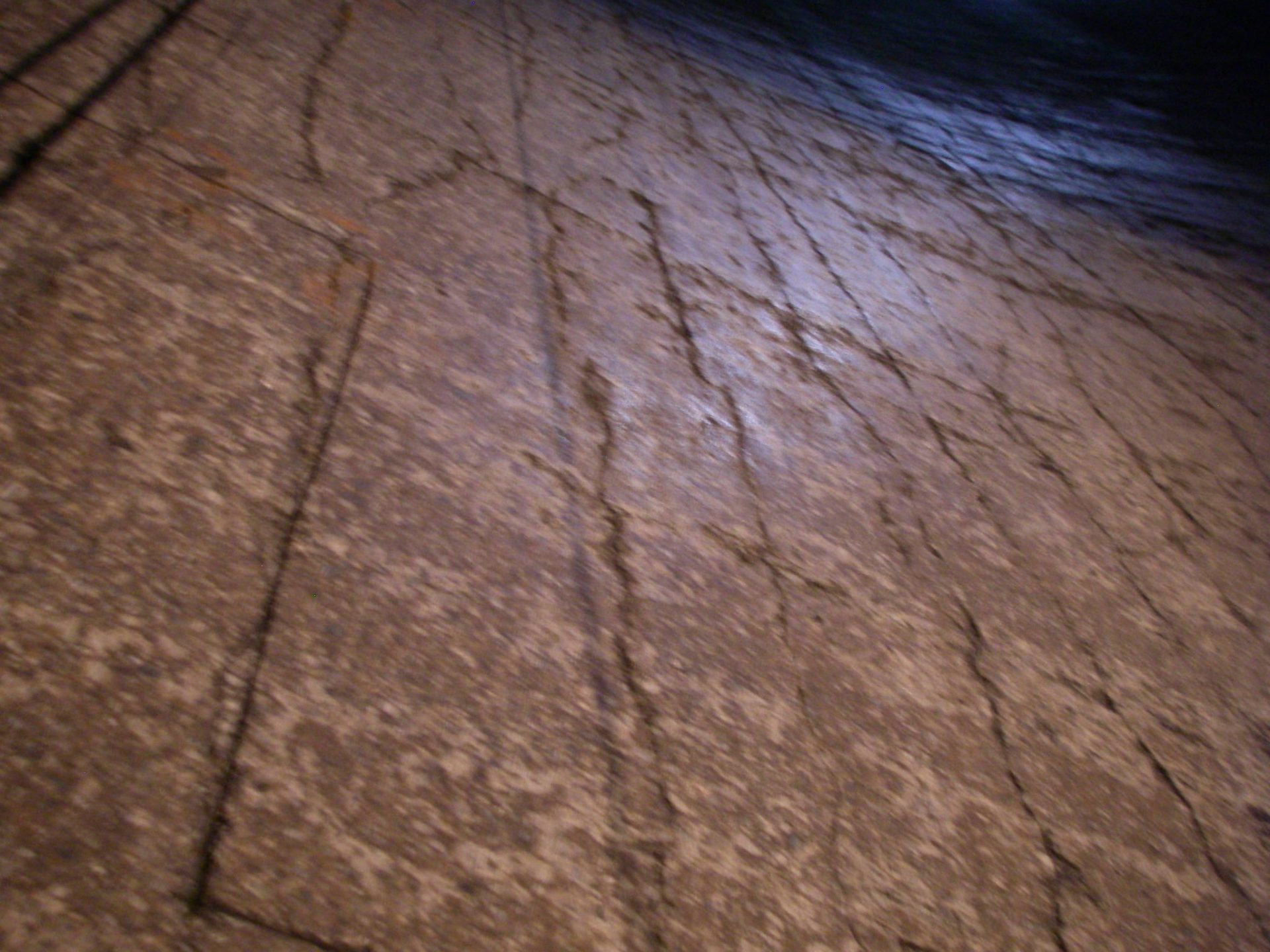
Generally, failure of equipment in industrial facilities does not make the national news unless it is a major disaster or, unfortunately, human lives have been lost. However, such failures are not uncommon, and silos represent a considerable percentage of the total amount of failures in industrial plants where bulk solids are handled. Silo failures are not necessarily catastrophic; they may occur as distortions or deformation in the shell of metal silos or as visible cracks in the walls of concrete silos. Certainly, the complete collapse of the silo structure is the extreme case, but those non-catastrophic failures may be the prelude to a much larger event in the near future.