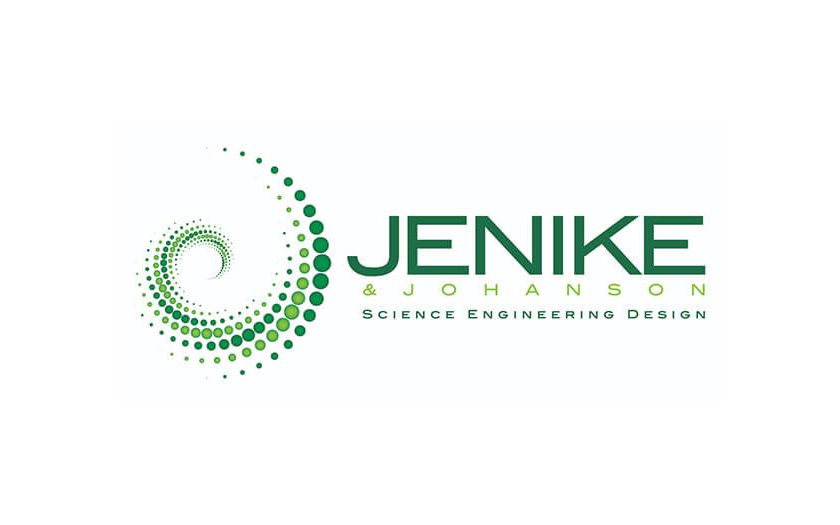
Earlier in the year there was some media focus on fatalities in grain silos, mostly on farms. At the time we had some internal discussions on safety and J&J’s unique perspective on it – we are in a lot of plants and see many silos, often from the inside. The very recent tragedy at an animal feed plant in Omaha brought it back to my mind. The cause of the Omaha Plant fire/explosion/structural collapse has not been identified at the time of writing- but my heart goes out to the victims and their families and friends.
Silo and bulk solids safety have a number of unique challenges. I thought it might be good to briefly touch on and share just a few of the hazards that I see as important and specific to silos and bulk solids.
Structural Issues
Catastrophic silo structural failures are very rare, fortunately. But when one does happen it can have severe consequences. Silos are typically not redundant structures- if a critical weld is improperly made or worn away, or a beam web corrodes to nothing and fails, there are usually no alternate load paths designed-in, and failure results.
Ask yourself; is this silo (that we work under!) in disrepair? If so, have a Professional Engineer with structural evaluation experience in silos conduct an inspection. Corrosion, leaking, buckling are all definite indicators of a problem. That it has not fallen down yet should never be taken as evidence of structural soundness!
The silo condition is good but -are you handling the material the silo was designed for, and in the manner intended? This is highly relevant if you are re-purposing an existing silo, installing a new feeder, or doing any significant modification, especially one that changes the flow pattern. If a new material, have the (new) material tested for flow properties and get that PE involved.
Any silo should be inspected, inside and out on a regular basis, under the supervision of a Professional Engineer. Wall thicknesses should be spot checked, at a minimum. The cone to cylinder weld (if you have one) should be carefully inspected. Mass flow silos will wear, and the wear rates vary widely depending on the application, from inches per eon to inches per year. Non-mass flow silos can corrode. Know and document the condition of yours, mass flow or funnel flow.
Entry
Silos are confined spaces. OSHA/MSHA have pretty strict guidelines for enclosed space entry, for good reason. Follow the OSHA or MSHA guidelines as applicable, and any specific to your facility. For silo entries I would emphasize the following as a minimum-
- Make sure there is no significant material adhered to a wall or ceiling that could fall on personnel. If there is, get it cleared out or hire a professional before entering the silo
- Even if you are extremely confident that your silo has no air quality problems, have the air checked before entry for hazardous gases and O2 content, and always carry an O2 monitor with you.
- Never enter a silo with material in it and walk on the material surface, even with safety ropes attached. Should you get buried, the ropes will pull you apart, not out. Solid appearing surfaces can have voids beneath.
- Before entry, follow lockout/tag out procedures for any/all equipment moving material into and out of the silo, air cannons, etc.
- When in a silo have someone monitor you from outside the silo. Have a radio for communicating with them and other people in your team. Due to echos and the general acoustic environment of a silo interior, talking or yelling is usually non-functional communication. Most places I have been in had me on a cable, so I could be winched out if needed.
- Going into a silo is hard work, at least from a roof or side hatch entry. Expect to be physically challenged.
Arching
Silos arch at outlets, and are typically dealt with by hammering on the hopper wall near the outlet. While usually not life threatening, injuries due to use of sledge hammers in such situations is not uncommon. From a safety perspective, it is definitely never recommended to open doors or hatches below the arch and attempt to get material flowing. Material flowing/flooding happens very fast, and is very dangerous. The skirt area of a silo can be filled in seconds, and the flood event can cause a structural collapse. If the material is hot- even worse, if that is possible. If you have continual arching problems, it should be reviewed as a primary safety issue, not just a process hassle. A redesign and rework of the outlet to eliminate arching is the safe approach -and often extremely cost effective.
Dust explosions and fires
If you are handling a material that has even the slightest ability to burn, review (or re-review) your entire process in light of a dust explosion hazard. MSDS information, especially for older data sheets, may lack information or not emphasize the hazard for materials that could be involved in an explosion or conflagration. Verify there is no material buildup on floors, light fixtures, beam flanges, etc that could end up air-born in a “what could go wrong” analysis and cause a larger ignited event. If you are filling a silo with a flammable material, it should likely have properly engineered explosion vents or other means of engineered protection.
If you have a question about a particular structural problem, [hs_form id=”1″]