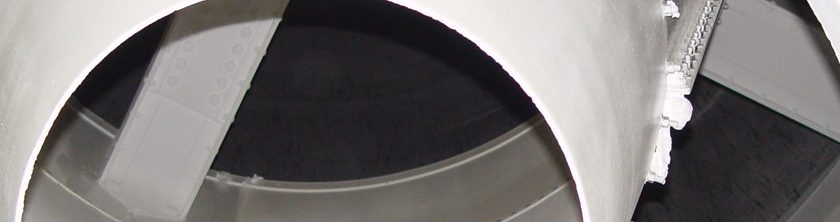
The answer to this riddle may not be obvious, but, it is quite simple…the hopper and lampshade have the same angle! This is shown in the graphic.
As with a lampshade (see “A”), a hopper must be made economically. Consequently, a 60º angle (see “B”) for a conical hopper is most commonly manufactured due to its simplicity, accuracy, and least amount of waste generated during fabrication.
The 60º cone for a silo or bin (see “C”) is derived from a semi-circle (see “D”) with a smaller cut-out for the required outlet; it is then rolled into a cone shape (see “E”). With this, the fabricator can quickly make two identical hoppers at 60º with no scrap other than the outlet cut-outs!
Unfortunately, though the 60º cone is attractive economically to fabricate, it generally will not allow for most powders and bulk solids. As a result, a discharge pattern will occur, often yielding flow problems such as arching, ratholing, powder flooding, and segregation.
If your material has any of these characteristics, then a mass flow hopper should be selected:
1) fine powder (average size < 100 US mesh or 150 μm)
2) prone to arching and ratholing
3) prone to caking or spoilage
4) segregation tendencies
If your material does not have any of these characteristics, then a funnel flow hopper may be acceptable. Mass flow hopper angles can easily be determined through bulk material flow testing. Additionally, cone shaped hoppers are not the only geometries that can provide mass flow. Wedge shapes and transition hoppers can also be designed for mass flow provided the surface selected allows flow of the bulk material against the hopper walls.
At Jenike & Johanson, our responsibility is to assist you with selecting the most economical, practical, safe, and efficient storage and handling solution – we are not in business to sell you mass flow hoppers. [modal_contact link_text=”Contact us”] if you have a question about hopper application or whatever else may be on your mind. Some “free” advice…leave the 60º angle selection for the lampshades!