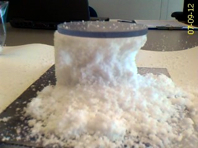
The Need
SABIC Innovative Plastics was undergoing a major expansion of their GTX resins process at the Noryl plant in Bergen Op Zoom Netherlands. The expansion included a much more automated blending and extrusion system which would provide dramatic improvements in efficiency, product consistency, and rapid changeovers. They anticipated one of the blend components for their new resins would be very poor flowing and were concerned that the anticipated results may not be realized.
The new system had to avoid flow problems in order to be successful. The SABIC design team wanted to avoid costly delays and any quality or productivity issues with the new resin especially as may be seen by the OEMs.
The Solution
Jenike and Johanson was requested to provide project engineering support to the team and advise as to how to handle the materials to ensure reliable, consistent flow. Our approach was to measure the relevant flow properties of the additives. Included in this analysis was the consideration of volatile content, and elevated processing conditions that contributed to the poor handling nature of the materials. This provided the design basis for developing hopper functional designs of feed options to achieve highly accurate dosing in a loose free-flowing consistency at a rate of 11 kg in 10 seconds, intermittently, batch-after-batch.
The Result
The expansion was successfully implemented. Acceptance batches of the new grade were made available to the OEMs. By fall of 2009, full production was underway with the new resin supplying a substantial weight savings that would reduce fuel consumption by an estimated 530 million liters per year.