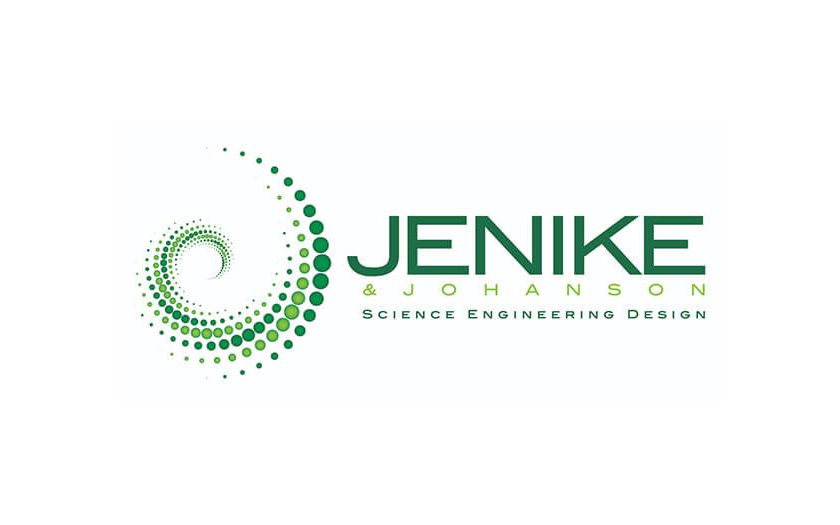
Vibrators are commonly used in many industries as “flow aids” or “flow promoters” for bulk solids. The chronology of vibrator use often goes like this: 1) a particular bulk solid is put inside a bin without regard for the bulk solids’ flow properties or bin design; 2) flow problems (e.g. arching, ratholing) arise; 3) someone nearby happens to have a vibrator they could use to get the material flowing again…
Of course I don’t have to tell you that a properly designed bin could have avoided the flow problems from the start, but for some this is a lesson learned the hard way. Having been to quite a few bulk solids processing plants, whether it is in the pharmaceutical, mining, or coal industry, I’ve seen vibrators of different types and sizes used with varying degrees of success. And asking operators and plant engineering personnel about vibrator use almost always elicits the same response: “we tried it out to see what would happen and tinkered with it until it worked”. Tinkering entails changing the size, amplitude and frequency of vibration, location, and number of units, and “worked” is usually taken very liberally. With all these variables the DOE matrix can be large. Add to this, some bulk solids change their flow characteristics when exposed to vibration, and bulk solid type needs to be thrown into the laundry list of variables.
For some materials and applications the use of vibrators make the problems they are supposed to fix worse or they can create new problems that were not present before. For example, exposing a compressible material to vibrations can significantly increase their cohesive strength making the outlet dimensions required to avoid a bridge very large and possibly making gravity flow impossible. Fine powders can be fluidized when exposed to vibrations causing flooding or flushing of powder. Vibration can also induce segregation or make it worse. From a structural perspective if the bin or silo is not designed to withstand sustained vibrations, adding a vibrator to the hopper can create and/or propagate cracks increasing the risk for structural failure.
One of the most common vibrator mistakes is to leave the vibrator on while the gate below the hopper is closed or the feeder is not operating – with nowhere to go the material has no other choice than to pack; increasing its cohesive strength.
I would love to hear your vibrator stories, the good, the bad, and the ugly…