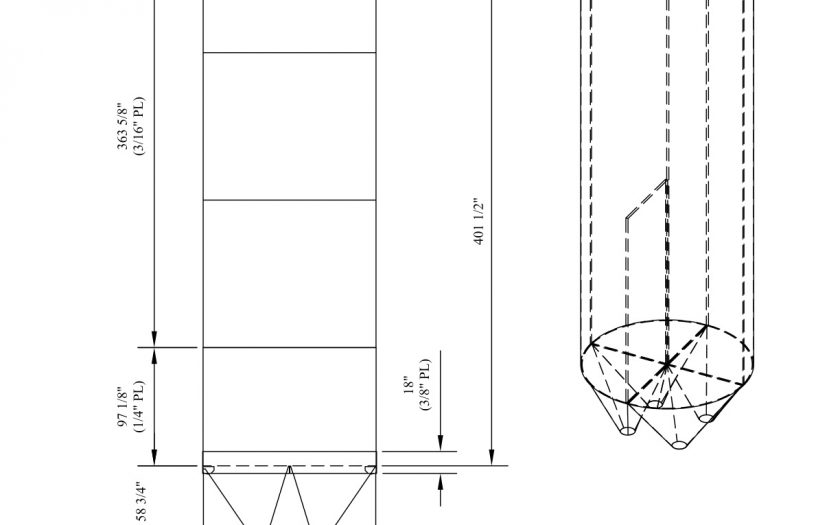
Have you ever heard of or come across a silos enthusiast or hobbyist? Probably not, unless you know someone working for Jenike & Johanson! No wonder, silos are not the most exciting or appealing object for appreciation. Silos are plain, do not move or have any moving parts, in contrast with the fast moving fighter jets, robots or cars. During the discharge process of a silo, the contents will move, however, so slowly that for all intents and purposes this motion is ignored. Not surprisingly, engineers assume a quasi-static condition, which neglects any dynamics effects in the silo structural design. As a consequence, the silo is not usually an object of dynamics, but only of statics analysis, which presumes equilibrium. Is there a shortcoming in this design approach? Yes: failure to predict any of the silo transient structural motion or response. Why should you worry about the dynamics of a silo and its implications? Can you minimize or prevent these structural dynamics effects in your silos?
Some of the most commonly reported silo dynamics responses are silo quaking, silo thumping, silo honking or silo music. All of these fall under the category of vibration, which can be described as a periodic motion or deformation of a silo or structural member. The vibration is characterized by amplitude and frequency of displacement or deformation. Typically, the fundamental frequency varies from about 1 Hz to as high as 50 Hz. The silo vibrations are commonly caused or induced by material discharge and, vary from an audible noise to a vigorous and unpleasant vibration of a floor attached to the silo. These vibrations may be harmless, i.e., just a source of discomfort or nuisance, or could lead to fatigue structural failure or collapse, in the worst-case scenario.
Dynamics analysis can be performed to solve Newton’s Laws of Motion to predict the motion or response of mechanical system parts when subjected to external forces. Accuracy of the predicted motions is commensurate with how well the dynamics physical properties of the parts, internal interaction forces and external forces can be characterized. As an example, researchers at MIT have built a cheetah robot that is capable of running and jumping over obstacles randomly thrown into its path (Jennifer Chu | MIT News). At first sight, the complexity of the robot dynamics is intimidating, however, once each moving part is identified and characterized, the equations of motion can be solved to accurately predict the movement of the robot. Unfortunately, unlike the robots, the dynamics analysis of a discharging silo presents an enormous challenge because the identification of moving parts and characterization of the interaction forces are not so obvious. The silo structure and the discharge equipment, e.g. feeder or valve, can be dynamically characterized, i.e. determine its mass and stiffness distribution. Weight is the external driving force during the discharge, so the external force is known. However, the bulk solid contents cannot be described as a single or even multiple distinct bodies. The content mass is constantly moving, deforming, failing internally in shear, compressing and expanding and, also interacting with the silo wall through normal and shear pressure. Hence, a dynamics analysis of a discharging silo cannot be conducted, analytically or numerically, following the normal procedure.
Simplified dynamics silo models have been devised and utilized to predict vibration in silos with varying degrees of success for particular types of materials. No objective and systematic silo analysis procedure has been established to predict the dynamics response. However, assessment of some of the factors, that are known to cause or exacerbate vibration, can help to minimize or prevent vibration. These include:
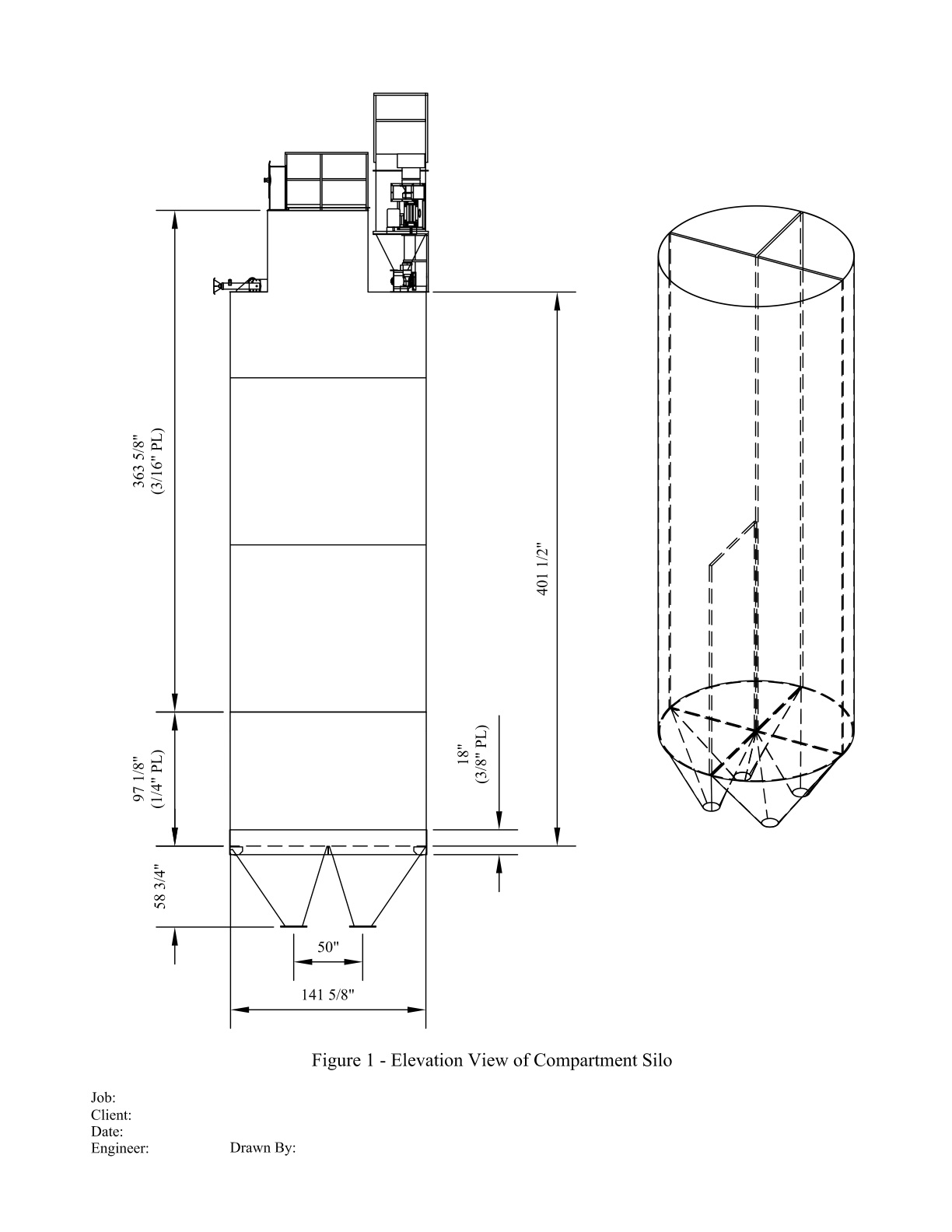
- Flow pattern (mass flow, funnel flow, border line)
- Slip-stick wall friction and internal friction
- Bulk solid is dense, frictional, incompressible and free flowing
- High aspect ratio bins, i.e. high H/D
- Material level
- High discharge rates
- Excessive high pressure concentrations
- Excitation by gate or feeder
Despite the engineering world’s resistance to seeing silos and their contents as a dynamic system, we do recommended a dynamics assessment of the structural system (bin and supporting structure) if vibration is suspected. In conclusion, knowing your material flow properties, the flow pattern, silo geometry and structural characteristics and considering the above will help you avoid conditions that can lead to silo vibration.
Contact us at Jenike & Johanson and we can help you ensure a quiet & well running silo.