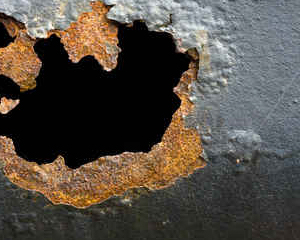
You may have heard of silo failures around the globe. Why do such failures still occur? The reasons are varied but generally one or more of the following:
- Design Constraints: Loads exerted on silo structures are not well defined in design codes.
- Mistakes are sometimes made during construction that may go unnoticed until the silo fails.
- Alterations are often made to silos without first evaluating the consequences to the structure.
- Maintenance of silos is often overlooked, postponed, or performed shoddily.
We will discuss here one common cause of failure: corrosion, which weakens the metal shell in bins and silos. Corrosion can be defined as the degradation of a material due to a reaction with its environment. Metals in bins and silos corrode because they are used in environments where they are chemically unstable. A corroded metal loses its strength and after a while, loses its shape too; in short, it loses the ability to what it was designed to do. Damage due to corrosion is not always uniform in nature but may be localized (see Fig. 1) causing premature failure or damage.

Metal storage silos are prone to failure by thickness loss due to corrosion; buckling strength of axially compressed cylinder shells depend on their r/t ratio (r = radius and t = thickness of shell). Thickness loss in the shell due to corrosion increases the r/t ratio, and shells with larger r/t ratio have a lower capacity against buckling strength. Similarly, hoop strength in the metal shell reduces due to the net area reduction caused by corrosion.
We have been involved in projects where moisture in the bulk solids reacted over a period of time with the silo metal and led to corrosion causing thickness loss and, eventually, catastrophic failure of the silo structure with significant loss of property and product. In our experience, corrosion has been a serious damaging ingredient for metal silos and cannot be overlooked. Therefore, if you have metal silos storing moist bulk solids, it is important to:
- Perform regular inspections to check for signs of corrosion.
- Perform periodic ultrasonic thickness measurements as part of your maintenance procedures.
- Do not ignore signs of distress in silos. Distortion is an early warning of potential failures in bins and silos.
If you have concern about your metal silos especially when you have moisture in your bulk solid, certainly we can help you to evaluate the conditions of your storage system and avoid potential failures.