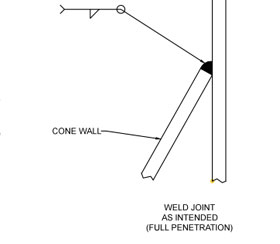
Co-Author: Jesús Chávez Sagarnaga
My definition of “hopper” is a sloped wall converging structure suspended along its top edge from the vertical wall portion of the bin or silo. Hoppers can be conical, wedge, pyramidal or a combination of these shapes. These converging parts are necessary and provide a practical means of directing and concentrating the discharge of the bin/silo contents to a specific point where it can be efficiently handled. Flow problems aside, it is hard to think of bins and silos without hoppers. I am primarily talking about circular silos constructed of welded steel with conical hoppers for the purpose of this discussion, although it applies to the other types of hoppers as well.
Depending on the size of the silo, the converging structure must safely hold up its contents along with the contents of the cylinder section that it is attached to. The material in the cylinder above the hopper can press down with loads as high as 50%-70% of the bin/silo contents. Most conical hoppers are generally thin plate type structures that are welded to the cylinder shells, which can also be constructed from a thin plate or something heavier like a built-up ring girder. The thin hopper plate behaves as a tensile membrane structure that moves (strains) relative to the cylinder at the attachment point as the silo is filled and emptied.
The key issue here is the welded joint that is used to attach the hopper section (see figure above). We at Jenike & Johanson have inspected many of these type weld joints and found some of them to be improperly installed when the bin/silo was initially fabricated. The weld joint is typically specified during the design phase to have a complete penetration fillet weld, but because of the limited access to the joint during the welding process, the weld metal does not penetrate the thickness of the hopper wall and can be as little as half the thickness (see photo). This reduced cross-section at the weld creates high tensile stresses in the joint. Furthermore, the movements of the hopper shell as the bin/silo is filled and emptied can cold-work (fatigue) this joint to the point of failure. We have investigated past catastrophic failures and identified this mechanism as the root cause. This unnecessary scenario ends in equipment damage, facility shutdown and sometimes the loss of life. Often during the inspection, we observe cracks in the attachment joint before the complete (catastrophic) separation of the conical hopper occurs.
The hopper attachment joints on all bins and silos should be inspected during fabrication or construction, and then at some interval established after the first inspection. Jenike & Johanson recommends at minimum that a qualified structural engineer specialized in bin/silo structures visually inspects this important attachment joint. So the question is: Is the attachment of your hopper safe?