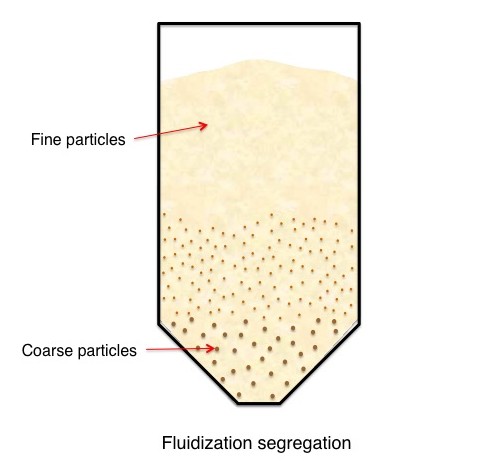
The Need
A contract pharmaceutical manufacturer was experiencing segregation of a fine powder blend during routine handling. A dense-phase pneumatic conveying system was used to transport the final blended material to a surge bin located above an encapsulation machine. The blend consisted of fine, active-rich, particles and several excipients with a substantially larger particle size. Though the blend did not experience segregation during pneumatic conveying, since the material was aerated during transport, the air trapped in the blend caused fluidization segregation to result during surge bin filling. This segregation yielded a concentration of fine particles (super potent) at the top surface of the blend after conveyance to the bin. Upon discharge, the fines would come out erratically and cause content uniformity issues in capsules.
The Solution
Jenike & Johanson engineers performed a root cause assessment of the blend handling system to determine why the problem occurs and then developed recommendations to minimize or eliminate the segregation. The problem was corrected by orienting the pneumatic conveying line to enter the bin tangentially, and the stainless steel hopper was polished to a smooth internal finish to promote mass flow discharge.
The Result
The pharmaceutical manufacture realized immediate improvement of blend homogeneity by implementing the relatively minor modifications. The low-cost solution provided a high return on investment.