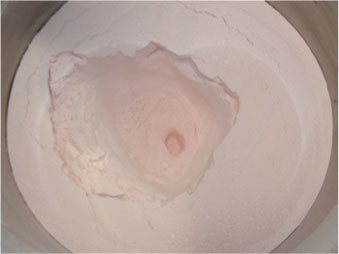
The Need
A pharmaceutical company was producing tablets from a granulation and did not experience flow or segregation problems during process development and validation. However, increased demand with the product required either faster press speeds or a secondary tableting press. The granulation had low segregation tendencies, but, it also flowed poorly through containers and press hoppers.
Jenike & Johanson was contacted to assist in determining the cause of the problems and to recommend a solution.
The Solution
While on-site at the plant, Jenike & Johanson engineers observed [popover image=”/your-need/poor-flow/hopper-flow-pattern-funnel-flow-cohesive-material/” link_text=”funnel flow” title=” ” content=”Discharge pattern occurring in silo, bin, bunker, or hopper” direction=”right”] discharge with the granulation in both the container and press hopper. Eventually, a rathole formed in each component, thereby requiring operators to poke at material to induce flow.
It was determined that a [popover image=”/your-need/poor-flow/hopper-flow-pattern-mass-flow/” link_text=”mass flow” title=” ” content=”Discharge pattern occurring in silo, bin, bunker, or hopper” direction=”right”] discharge pattern in both the portable container and press hopper would yield reliable, consistent gravity flow into the press paddle feeder, thus providing consistent tablet weights. Flow properties tests on the granulation were measured and the data were used to design new components that would promote mass flow.
The Result
Without modifications to the press (other than the hopper) or the granulation, the press speed was doubled and consistent tablet weights were achieved. Note that other attempts at measures of powder flowability, such as angle of repose, compressibility, or flow funnel times would not have provided any insight into the true cause of the problem nor how to solve it.